Il compensato è costituito da tre o più sottili strati di legno incollati tra loro con un adesivo. Ogni strato di legno, o compensato, è solitamente orientato con le venature perpendicolari rispetto allo strato adiacente per ridurre il ritiro e migliorare la resistenza del pezzo finito. La maggior parte del compensato viene pressata in grandi fogli piatti utilizzati nell'edilizia. Altri pezzi di compensato possono essere sagomati in curve semplici o composte per l'utilizzo in mobili, imbarcazioni e aeromobili.
L'uso di sottili strati di legno come mezzo di costruzione risale a circa il 1500 a.C., quando gli artigiani egiziani incollarono sottili pezzi di ebano scuro all'esterno di un cofanetto di cedro rinvenuto nella tomba del faraone Tutankhamon. Questa tecnica fu poi utilizzata dai Greci e dai Romani per produrre mobili pregiati e altri oggetti decorativi. Nel XVII secolo, l'arte di decorare i mobili con sottili pezzi di legno divenne nota come impiallacciatura, e i pezzi stessi divennero noti come impiallacciature.
Fino alla fine del 1700, i pezzi di impiallacciatura venivano tagliati interamente a mano. Nel 1797, l'inglese Sir Samuel Bentham presentò una domanda di brevetto per diverse macchine per la produzione di impiallacciature. Nelle sue domande di brevetto, descrisse il concetto di laminare diversi strati di impiallacciatura con colla per formare un pezzo più spesso: la prima descrizione di quello che oggi chiamiamo compensato.
Nonostante questo sviluppo, ci vollero quasi altri cento anni prima che i piallacci laminati trovassero usi commerciali al di fuori dell'industria del mobile. Intorno al 1890, i legni laminati furono utilizzati per la prima volta per la costruzione di porte. Con la crescita della domanda, diverse aziende iniziarono a produrre fogli di legno lamellare multistrato, non solo per le porte, ma anche per vagoni ferroviari, autobus e aerei. Nonostante questo crescente utilizzo, il concetto di "legno incollato", come alcuni artigiani lo chiamavano sarcasticamente, generò un'immagine negativa del prodotto. Per contrastare questa immagine, i produttori di legno lamellare si incontrarono e alla fine decisero di usare il termine "compensato" per descrivere il nuovo materiale.
Nel 1928, negli Stati Uniti furono introdotti i primi fogli di compensato di dimensioni standard di 1,2 m x 2,4 m (4 piedi x 8 piedi) per l'uso come materiale da costruzione generico. Nei decenni successivi, adesivi migliorati e nuovi metodi di produzione permisero al compensato di essere utilizzato per un'ampia varietà di applicazioni. Oggi, il compensato ha sostituito il legname tagliato in molti settori dell'edilizia e la sua produzione è diventata un'industria mondiale multimiliardaria.
Gli strati esterni del compensato sono noti rispettivamente come faccia e retro. La faccia è la superficie che deve essere utilizzata o vista, mentre il retro rimane inutilizzato o nascosto. Lo strato centrale è noto come anima. Nei compensati con cinque o più strati, gli strati intermedi sono noti come bande trasversali.
Il compensato può essere realizzato con legni duri, teneri o una combinazione dei due. Tra i legni duri più comuni ci sono il frassino, l'acero, il mogano, la quercia e il teak. Il legno tenero più comune utilizzato per produrre compensato negli Stati Uniti è l'abete Douglas, sebbene vengano utilizzate anche diverse varietà di pino, cedro, abete rosso e sequoia.
Il compensato composito ha un'anima composta da truciolato o legno massello uniti bordo a bordo. È rifinito con una superficie e un retro in compensato impiallacciato. Il compensato composito viene utilizzato quando sono necessari fogli molto spessi.
Il tipo di adesivo utilizzato per incollare gli strati di legno dipende dall'applicazione specifica del compensato finito. I fogli di compensato di legno tenero progettati per l'installazione all'esterno di una struttura utilizzano solitamente una resina fenolica-formaldeide come adesivo per la sua eccellente resistenza e resistenza all'umidità. I fogli di compensato di legno tenero progettati per l'installazione all'interno di una struttura possono utilizzare un adesivo a base di proteine del sangue o di proteine di soia, sebbene la maggior parte dei fogli di compensato di legno tenero per interni sia ora realizzata con la stessa resina fenolica-formaldeide utilizzata per i fogli per esterni. Il compensato di legno duro utilizzato per applicazioni interne e nella costruzione di mobili è solitamente realizzato con una resina urea-formaldeide.
Alcune applicazioni richiedono fogli di compensato con un sottile strato di plastica, metallo o carta o tessuto impregnato di resina, incollato sul lato anteriore o posteriore (o su entrambi) per conferire alla superficie esterna una maggiore resistenza all'umidità e all'abrasione o per migliorarne le proprietà di tenuta della vernice. Questo tipo di compensato è chiamato compensato sovrapposto ed è comunemente utilizzato nei settori dell'edilizia, dei trasporti e dell'agricoltura.
Altri fogli di compensato possono essere rivestiti con una tinta liquida per conferire alle superfici un aspetto rifinito, oppure possono essere trattati con vari prodotti chimici per migliorare la resistenza alla fiamma o alla decomposizione del compensato.
Esistono due grandi categorie di compensato, ciascuna con il proprio sistema di classificazione.
Una classe è nota come "edilizia e industriale". I compensati di questa classe sono utilizzati principalmente per la loro resistenza e sono classificati in base alla loro capacità di esposizione e al grado di impiallacciatura utilizzata su superficie e retro. La capacità di esposizione può essere interna o esterna, a seconda del tipo di colla. Le qualità dell'impiallacciatura possono essere N, A, B, C o D. La qualità N presenta pochissimi difetti superficiali, mentre la qualità D può presentare numerosi nodi e spaccature. Ad esempio, il compensato utilizzato per il sottofondo di un'abitazione è classificato "Interno CD". Ciò significa che ha una superficie C e un retro D e la colla è adatta all'uso in luoghi protetti. Gli strati interni di tutti i compensati da costruzione e industriali sono realizzati con impiallacciatura di qualità C o D, indipendentemente dalla classificazione.
L'altra classe di compensato è nota come legno duro e decorativo. I compensati di questa classe sono utilizzati principalmente per il loro aspetto e sono classificati in ordine decrescente di resistenza all'umidità: Tecnico (Esterni), Tipo I (Esterni), Tipo II (Interni) e Tipo III (Interni). Le loro impiallacciature superficiali sono praticamente prive di difetti.
Dimensioni
Lo spessore dei fogli di compensato varia da 1,6 mm (0,06 pollici) a 76 mm (3,0 pollici). Gli spessori più comuni sono compresi tra 6,4 mm (0,25 pollici) e 19,0 mm (0,75 pollici). Sebbene il nucleo, le fasce trasversali e la superficie frontale e posteriore di un foglio di compensato possano essere realizzati con impiallacciature di spessore diverso, lo spessore di ciascuna di esse deve essere bilanciato attorno al centro. Ad esempio, la superficie frontale e posteriore devono avere lo stesso spessore. Allo stesso modo, le fasce trasversali superiori e inferiori devono essere uguali.
La dimensione più comune per i fogli di compensato utilizzati nell'edilizia è di 1,2 m di larghezza per 2,4 m di lunghezza. Altre larghezze comuni sono 0,9 m e 1,5 m. Le lunghezze variano da 2,4 m a 3,6 m con incrementi di 0,3 m. Applicazioni speciali come la costruzione di imbarcazioni potrebbero richiedere fogli più grandi.
Gli alberi utilizzati per produrre compensato hanno generalmente un diametro inferiore rispetto a quelli utilizzati per produrre legname. Nella maggior parte dei casi, sono stati piantati e coltivati in aree di proprietà dell'azienda produttrice di compensato. Queste aree vengono gestite con cura per massimizzare la crescita degli alberi e ridurre al minimo i danni causati da insetti o incendi.
Ecco una tipica sequenza di operazioni per la trasformazione degli alberi in fogli di compensato standard da 4 x 8 piedi (1,2 m x 2,4 m):
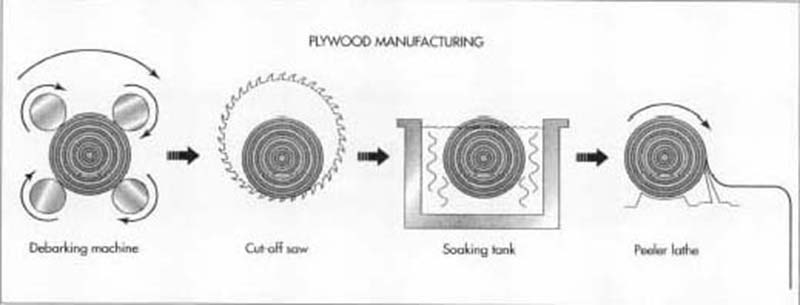
I tronchi vengono prima scortecciati e poi tagliati in blocchi da sfogliatura. Per tagliare i blocchi in strisce di impiallacciatura, vengono prima immersi in acqua e poi sfogliati in strisce.
1 Gli alberi selezionati in un'area vengono contrassegnati come pronti per essere abbattuti. L'abbattimento può essere effettuato con motoseghe a benzina o con grandi cesoie idrauliche montate sulla parte anteriore di veicoli a ruote chiamati abbattitori. I rami vengono rimossi dagli alberi caduti con le motoseghe.
2 I tronchi d'albero potati vengono trascinati in un'area di carico da veicoli a ruote chiamati skidder. I tronchi vengono tagliati a misura e caricati su camion per il trasporto alla segheria, dove vengono accatastati in lunghe pile chiamate "tavole di tronchi".
3 Man mano che i tronchi sono necessari, vengono prelevati dai piani di carico da pale gommate e posizionati su un trasportatore a catena che li porta alla scortecciatrice. Questa macchina rimuove la corteccia, tramite mole a denti affilati o getti d'acqua ad alta pressione, mentre il tronco viene lentamente ruotato attorno al suo asse longitudinale.
4 I tronchi scortecciati vengono trasportati nel mulino su un trasportatore a catena dove un'enorme sega circolare li taglia in sezioni lunghe circa 2,5-2,6 m, adatte alla produzione di fogli standard lunghi 2,4 m. Queste sezioni di tronco sono note come blocchi da sfogliatura.
5 Prima di poter tagliare l'impiallacciatura, i blocchi di sfogliatura devono essere riscaldati e immersi per ammorbidire il legno. I blocchi possono essere trattati con vapore o immersi in acqua calda. Questo processo richiede dalle 12 alle 40 ore a seconda del tipo di legno, del diametro del blocco e di altri fattori.
6 I blocchi di sfogliatura riscaldati vengono quindi trasportati al tornio, dove vengono automaticamente allineati e alimentati nel tornio uno alla volta. Mentre il tornio ruota rapidamente il blocco attorno al suo asse longitudinale, una lama a tutta lunghezza stacca un foglio continuo di impiallacciatura dalla superficie del blocco rotante a una velocità di 90-240 m/min. Quando il diametro del blocco si riduce a circa 230-305 mm, il pezzo di legno rimanente, noto come anima di sfogliatura, viene espulso dal tornio e un nuovo blocco di sfogliatura viene inserito al suo posto.
7 Il lungo foglio di impiallacciatura che fuoriesce dal tornio sfogliatore può essere lavorato immediatamente, oppure può essere immagazzinato in lunghi vassoi a più livelli o avvolto in rotoli. In ogni caso, il processo successivo prevede il taglio dell'impiallacciatura in larghezze utilizzabili, solitamente circa 1,4 m (4 piedi-6 pollici), per la produzione di fogli di compensato standard da 1,2 m (4 piedi). Allo stesso tempo, gli scanner ottici cercano sezioni con difetti inaccettabili e queste vengono tagliate, lasciando pezzi di impiallacciatura di larghezza inferiore a quella standard.
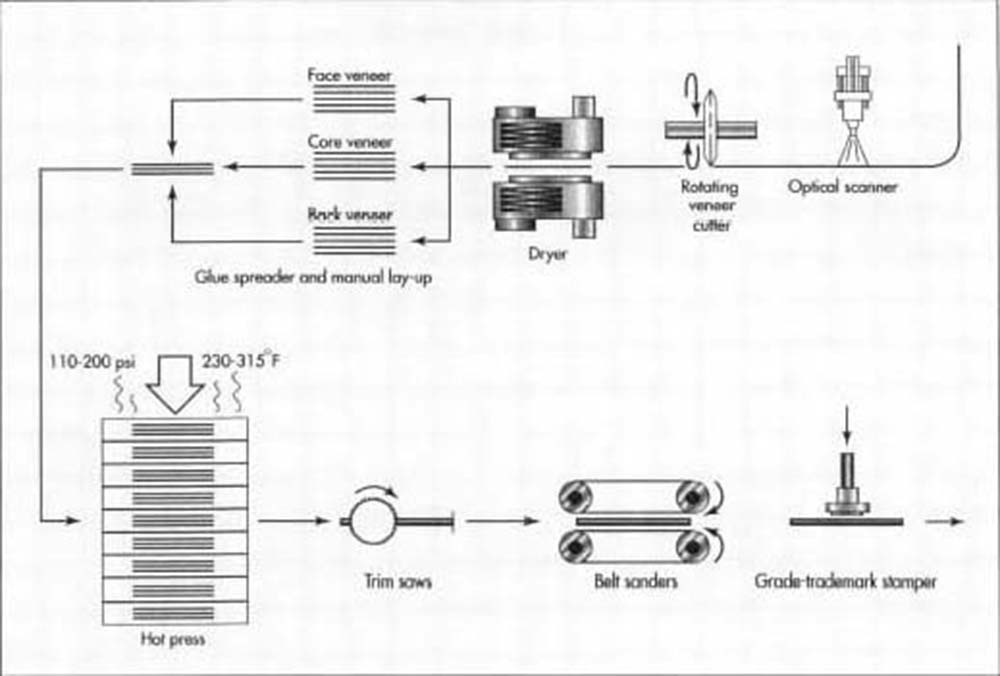
Le strisce di impiallacciatura bagnate vengono avvolte in un rotolo, mentre uno scanner ottico rileva eventuali difetti inaccettabili nel legno. Una volta essiccate, le impiallacciature vengono classificate e impilate. Sezioni selezionate di impiallacciatura vengono incollate insieme. Una pressa a caldo viene utilizzata per sigillare l'impiallacciatura in un unico pezzo di compensato, che verrà rifilato e levigato prima di essere marchiato con la classificazione appropriata.
8 Le sezioni di impiallacciatura vengono quindi smistate e impilate in base alla qualità. Questa operazione può essere eseguita manualmente o automaticamente tramite scanner ottici.
9 Le sezioni selezionate vengono inserite in un essiccatoio per ridurne il contenuto di umidità e consentirne il ritiro prima di essere incollate. La maggior parte delle fabbriche di compensato utilizza un essiccatoio meccanico in cui i pezzi si muovono continuamente attraverso una camera riscaldata. In alcuni essiccatoi, getti d'aria calda ad alta velocità vengono soffiati sulla superficie dei pezzi per accelerare il processo di essiccazione.
10. Man mano che le sezioni di impiallacciatura escono dall'essiccatoio, vengono impilate in base alla qualità. Le sezioni sottostanti presentano ulteriore impiallacciatura giuntata con nastro adesivo o colla per rendere i pezzi adatti all'uso negli strati interni, dove l'aspetto e la resistenza sono meno importanti.
11 Le sezioni di impiallacciatura che verranno installate trasversalmente (l'anima in fogli a tre strati o le fasce trasversali in fogli a cinque strati) vengono tagliate in lunghezze di circa 1,3 m (4 piedi e 3 pollici).
12 Quando le sezioni appropriate di impiallacciatura vengono assemblate per una specifica produzione di compensato, inizia il processo di disposizione e incollaggio dei pezzi. Questo può essere fatto manualmente o semiautomaticamente con macchinari. Nel caso più semplice di fogli a tre strati, l'impiallacciatura posteriore viene stesa in piano e passata attraverso una spalmatrice di colla, che applica uno strato di colla sulla superficie superiore. Le sezioni corte di impiallacciatura centrale vengono quindi disposte trasversalmente sopra il retro incollato, e l'intero foglio viene passato attraverso la spalmatrice di colla una seconda volta. Infine, l'impiallacciatura anteriore viene stesa sopra l'anima incollata e il foglio viene impilato con altri fogli in attesa di essere inserito nella pressa.
13 I fogli incollati vengono caricati in una pressa a caldo a più aperture. Le presse possono gestire 20-40 fogli alla volta, con ogni foglio caricato in una fessura separata. Una volta caricati tutti i fogli, la pressa li comprime insieme a una pressione di circa 110-200 psi (7,6-13,8 bar), riscaldandoli contemporaneamente a una temperatura di circa 230-315 °F (109,9-157,2 °C). La pressione assicura un buon contatto tra gli strati di impiallacciatura e il calore fa sì che la colla si indurisca correttamente per la massima resistenza. Dopo un periodo di 2-7 minuti, la pressa viene aperta e i fogli vengono scaricati.
14 I fogli grezzi passano poi attraverso una serie di seghe, che li rifiniscono alla larghezza e lunghezza finali. I fogli di qualità superiore passano attraverso una serie di levigatrici a nastro larghe 1,2 m, che levigano sia la superficie che il retro. I fogli di qualità intermedia vengono carteggiati manualmente per eliminare le aree ruvide. Alcuni fogli vengono fatti passare attraverso una serie di lame circolari, che incidono delle scanalature poco profonde sulla superficie per conferire al compensato un aspetto strutturato. Dopo un'ispezione finale, eventuali difetti rimanenti vengono riparati.
15 I fogli finiti vengono timbrati con un marchio di qualità che fornisce all'acquirente informazioni sul grado di esposizione, la qualità, il numero di stabilimento e altri fattori. I fogli con lo stesso marchio di qualità vengono legati insieme in pile e trasferiti al magazzino in attesa della spedizione.
Proprio come per il legname, non esiste un compensato perfetto. Tutti i pezzi di compensato presentano un certo numero di difetti. Il numero e la posizione di questi difetti determinano la qualità del compensato. Gli standard per i compensati da costruzione e industriali sono definiti dallo Standard di Prodotto PS1, redatto dal National Bureau of Standards e dall'American Plywood Association. Gli standard per i compensati di legno duro e decorativi sono definiti dallo Standard ANSIIHPMA HP, redatto dall'American National Standards Institute e dall'Hardwood Plywood Manufacturers' Association. Questi standard non solo stabiliscono i sistemi di classificazione per il compensato, ma specificano anche i criteri di costruzione, prestazione e applicazione.
Sebbene il compensato utilizzi gli alberi in modo piuttosto efficiente – essenzialmente smontandoli e riassemblandoli in una configurazione più resistente e utilizzabile – il processo di produzione genera comunque notevoli sprechi. Nella maggior parte dei casi, solo circa il 50-75% del volume di legno utilizzabile di un albero viene convertito in compensato. Per migliorare questa percentuale, sono in fase di sviluppo diversi nuovi prodotti.
Un nuovo prodotto è il pannello a scaglie orientate (OSB), che si ottiene sminuzzando l'intero tronco in scaglie, anziché rimuoverne l'impiallacciatura e scartarne il nucleo. Le scaglie vengono mescolate con un adesivo e compresse in strati con le venature che corrono in un'unica direzione. Questi strati compressi vengono quindi orientati ad angolo retto l'uno rispetto all'altro, come il compensato, e incollati tra loro. Il pannello a scaglie orientate (OSB) è resistente quanto il compensato e costa leggermente meno.
Data di pubblicazione: 10-08-2021